
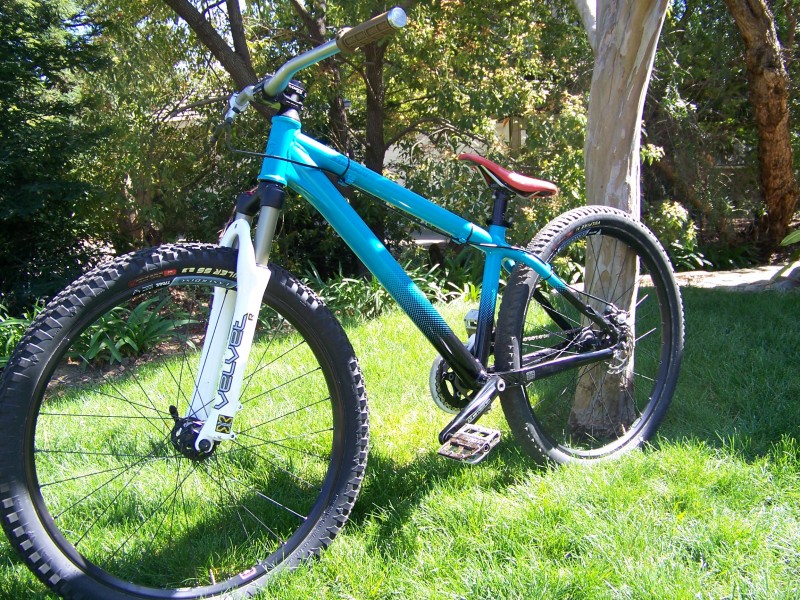
Best of luck to you.ĪCCURACY_LOWER_BOUND - value (between 1.0e-6 and 1.0e-4). Here is some data that you might want to check with the originators of the pro/e data. That's the same reason why parametric modeling will never be downward compatible.okay A-CAD users stop submitting enhancement requests. For example, Pro/e has a variable section sweep and SWx doesn't so those features will not translate. One thing to keep in mind is not all features cross over between the two systems. I've imported a lot of Pro/e files into SWx via STeP and feature works.
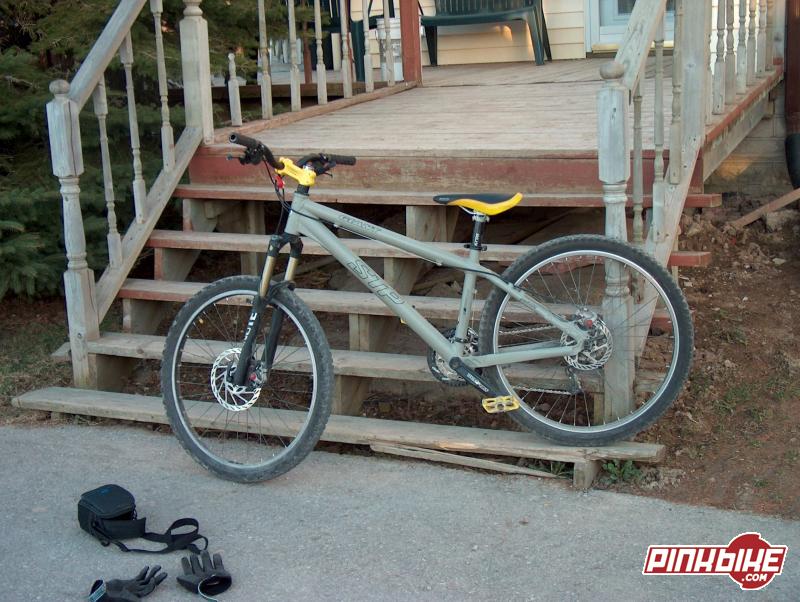
RE: Large IGS and STP files in SW 2005 CorBlimeyLimey (Mechanical) 4 Oct 06 19:35 They'll bring you down to their level and beat you with experience every time. Managers instead should hire cad-savvy technicians to check models before introducing them to engineering systems. Most industrial designers don't have the patience for this type of work. Users of hybrid modeling systems can reduce accuracy errors by closing gaps between surfaces before importing them into solid-modeling programs. Or they can cause translations to programs such as AutoCAD or CATIA to fail. Once incorporated into the solid, these large gaps can be passed through to STEP or IGES models or they can stall FEA, NC, and rapid prototyping programs. Surface-modeling programs - such as Alias Studio or Pro/Designer, don't care about gaps between surfaces.
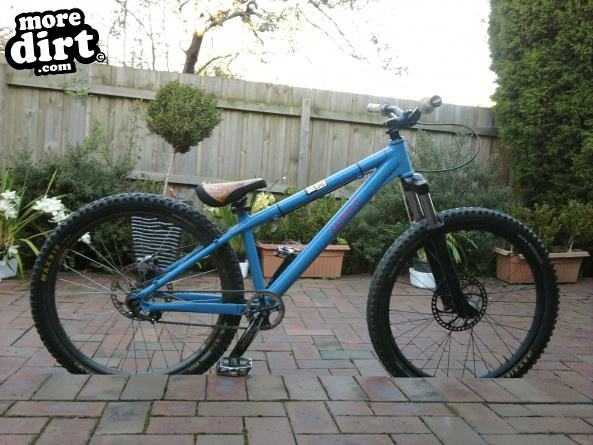
Large gaps also can be introduced into Parasolid models by importing surfaces. Tolerant systems, such as those based on Parasolid, will sew models with large gaps. In these cases, translations simply fail, and it is up to the Pro/E user to tighten down the tolerance, regenerate the model, and try again. Solid-modeling programs with fixed tolerances generally won't be able to sew up models with such large gaps. ITI found one instance - in an aircraft engine housing - where a gap exceeded one millimeter. Because of its relative-tolerance strategy, Pro/Engineer can leave large gaps between large faces. There are a couple of ways that large gaps can creep into models. But such gaps can cause translations to fail and can stall NC, rapid prototyping, and finite-element applications. The reverse is also true: Models from fixed tolerance systems may be unacceptable to Pro/E or UG if they contain gaps that are too large.ĭesigners creating CAD models do not generally notice gaps between adjacent faces or between faces and their associated edge curves that exceed the allowable tolerance of their CAD programs. Models coming from Pro/Engineer or Unigraphics may have gaps that aren't acceptable to CATIA or SolidDesigner. The difference in tolerance strategies causes problems when translating geometry from one system to another. The Parasolid kernel employed by Unigraphics, SolidWorks, Solid Edge, and Microstation employs a concept called "tolerant modeling." The tolerance is fixed, but larger gaps may be permitted on a face-by-face basis. Most systems enable users to change this default value but the vendors strongly discourage such changes with scary disclaimers of what might happen to the CAD program's behavior. The size of all gaps in all models is limited to the same default value. Most systems, including CATIA version four, Computervision's CADDS, and Spatial Technology's ACIS (employed by AutoCAD, Ashlar Vellum, IronCAD, SolidDesigner, and TurboCAD), employ a fixed tolerance model. Unfortunately, no other major CAD firms have adopted this strategy.

The relative tolerance model is a clever one, and it enables Pro/E to run fast. So for large models, such as jet engines, Pro/E allows larger gaps, while for small models, such as watch parts, only small gaps are permitted. The maximum gap is a fraction of the total model size. Pro/Engineer employs a variable tolerance model. Unfortunately, different systems employ different strategies for computing this tolerance. In such cases, the user might receive a message that the model is "corrupted." Consequently, all systems employ a strategy for computing the maximum allowable gap, or "tolerance zone," between an edge and the two faces it bounds. The system can no longer distinguish the inside of a part from the universe around it. If the gaps between edges and faces become too large, solid-modeling programs can become confused about the boundaries of the model. Here is some information from an article I got from the web What MCAD package is the data native to? It could be that the data contains a lot of surfaces or complex geometry.
